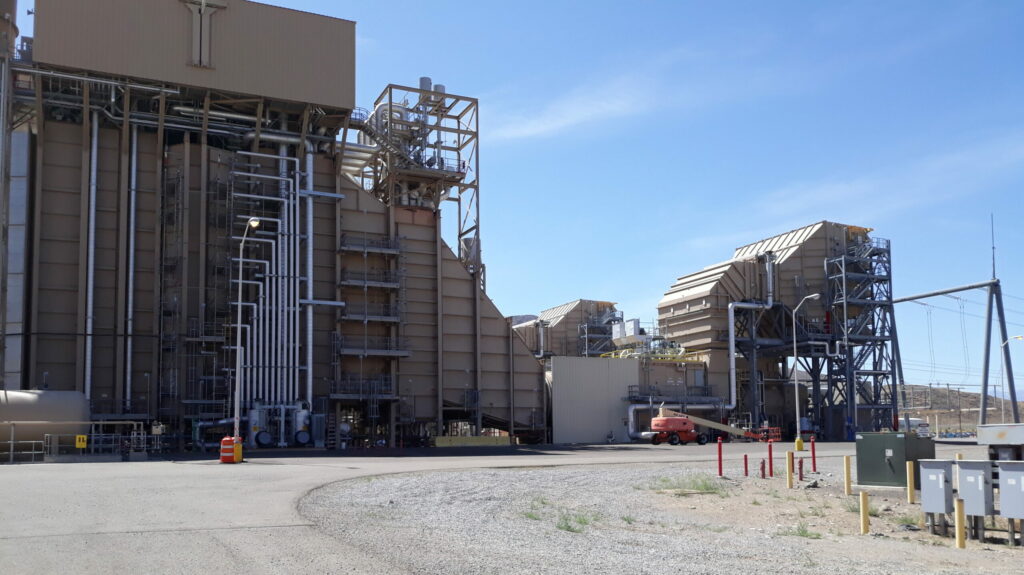
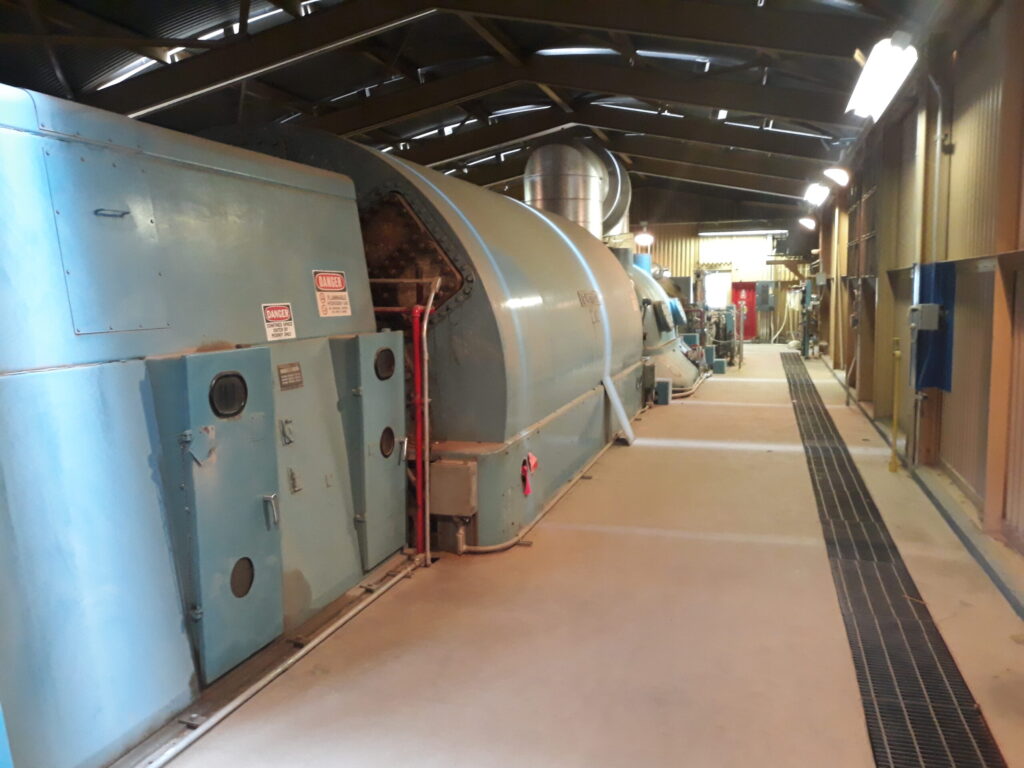
Engineering Intern
My first internship during my time at the University of Nevada, Reno, was at NV Energy’s Tracy Generating Station just East of Reno, NV. I worked here over the summer, the same summer I designed and constructed my Off-grid solar setup. I guess I could call it the summer of power generation?
Anyways, I very much enjoyed my time as an Intern there, and got to learn about a lot in the industry and work on a few projects.
Unit 4/5 Phosphate Feed System Upgrade
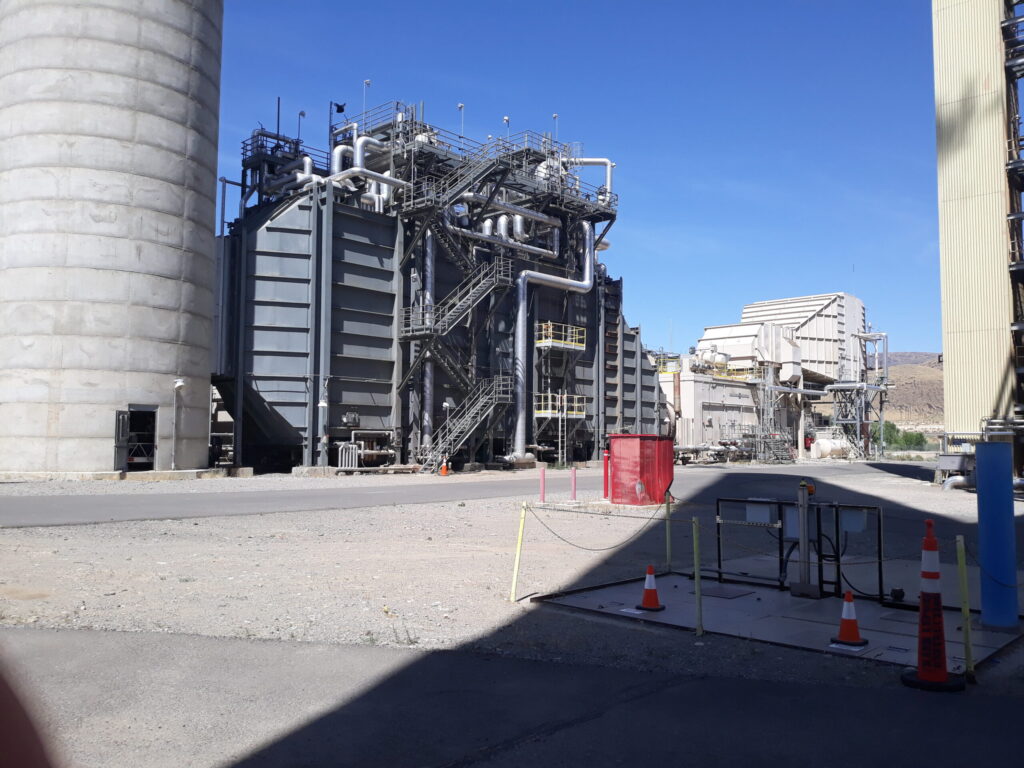
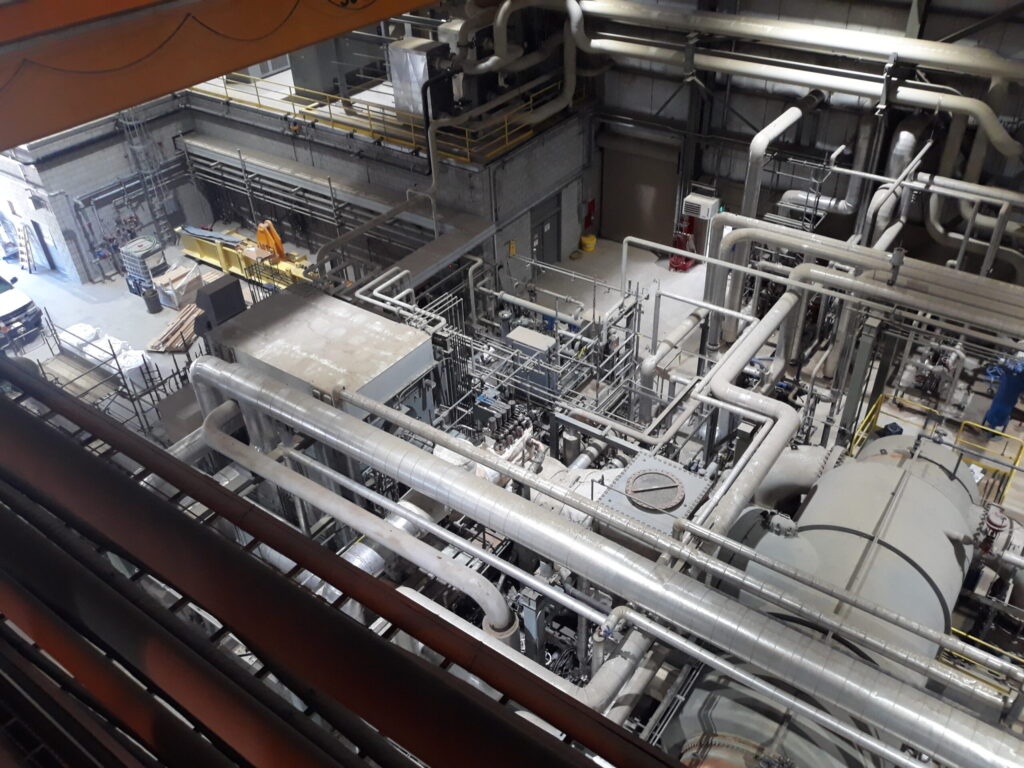
The phosphate feed system on Unit 5 is used on startups to treat the water used in the steam turbine to help inhibit corrosion and other unwanted degradation. The original system was difficult to use and dose the system properly. Spills happened often, and the system was slow to use as the dosing canisters were too small. It was was determined that something better was needed. The plant technicians had ordered some parts for an upgrade – like the sight glasses / dose measuring canisters and a new storage system for delivered phosphate before I was hired on, but did not have a complete plan.
The project was handed off to me, and I was to finish the design including how to transfer the phosphate to the dosing system, the piping setup (including P&ID changes), and some electrical. After gathering input from plant technicians, and reviewing P&IDs I was able to come up with a solution and ideal setup. Per input from the technicians I had opted for special chemical resistant PVC that was on-hand, but my engineering lead did not like the idea and wanted something that was originally spec’d for the unit. Technicians did not like this because the original spec called for welded stainless which would be costly and difficult. Fortunately, I found a solution that both could agree on – stainless tubing. It was relatively inexpensive and easy to assemble, and I was able to find such tubing spec’d for the unit in other areas and thus use an existing spec for the unit.
I also came up with a solution for pumping the phosphate to the dosing system – which ended up being a bit of a challenge. I determined that the pump the technicians had picked out would not be sufficient (too slow), and had to find a pump that would both pump fast enough, but not too fast, and be easy to implement. In addition, it couldn’t be costly. I settled on a somewhat unorthodox solution – but one that met all the requirements. The system was also designed with fail-safes in mind, so that in the event something went wrong major problems (such as overflows) would be mitigated. Conditions such as where the pump was left on inadvertently and unexpected pressures were considered and passive measures were implemented where possible. In addition, the pump I chose was meant to pump fast enough that a technician could stand watch the entire time during startup, to mitigate the possibility of it being left on as they did other things while it was on, yet still be able to pump a precise amount easily. In the end, the changes were approved and work started on the new setup. Unfortunately the summer was over before it was completed so I didn’t get to see it put to use.
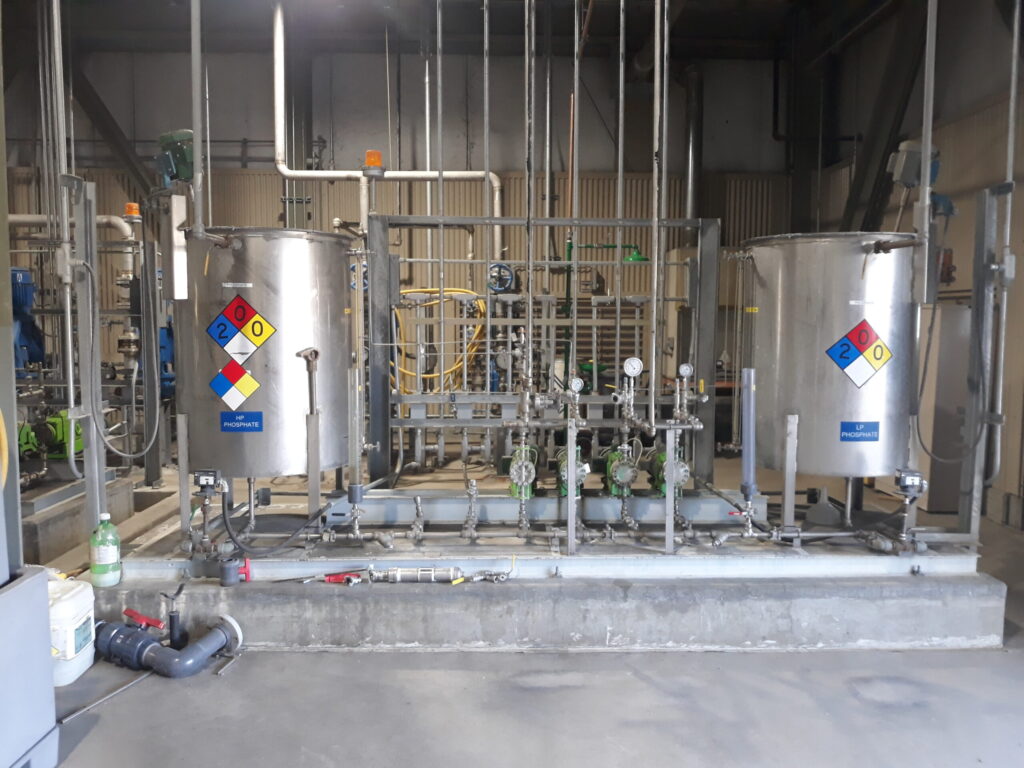
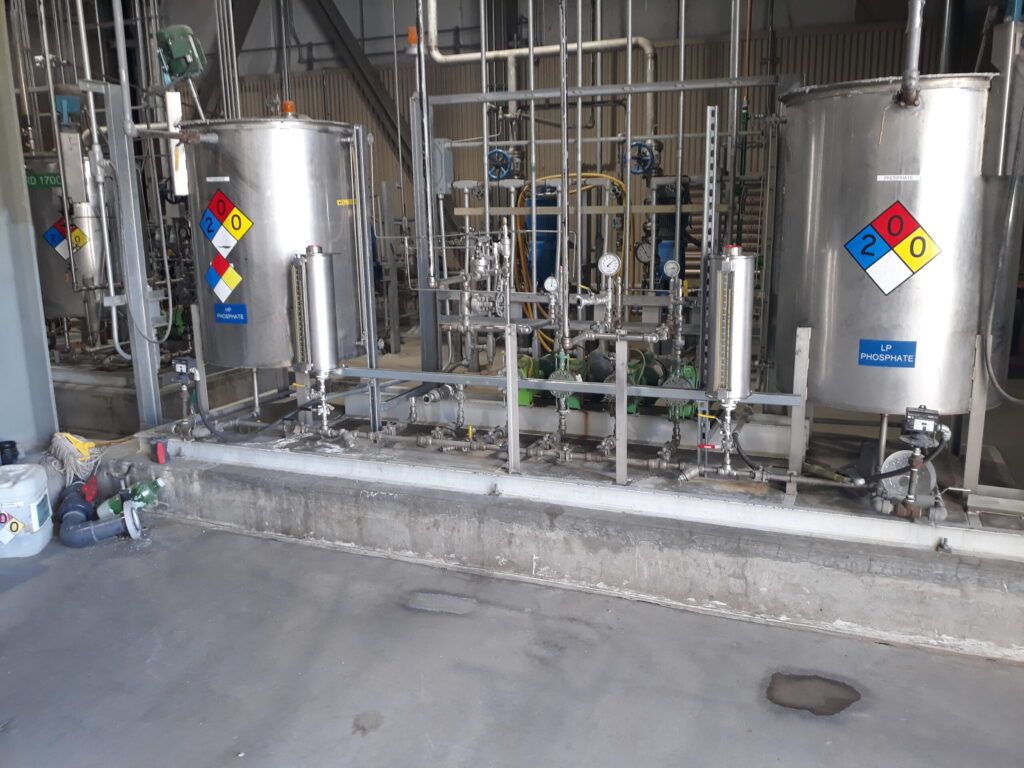
Plant Piping Inspection
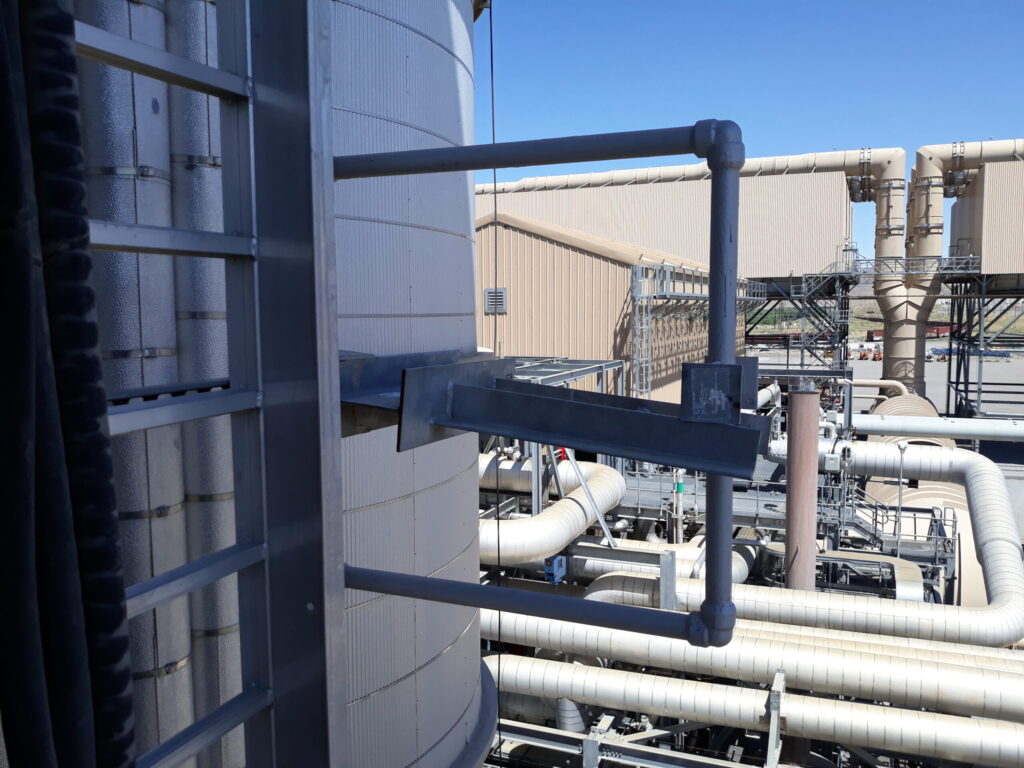
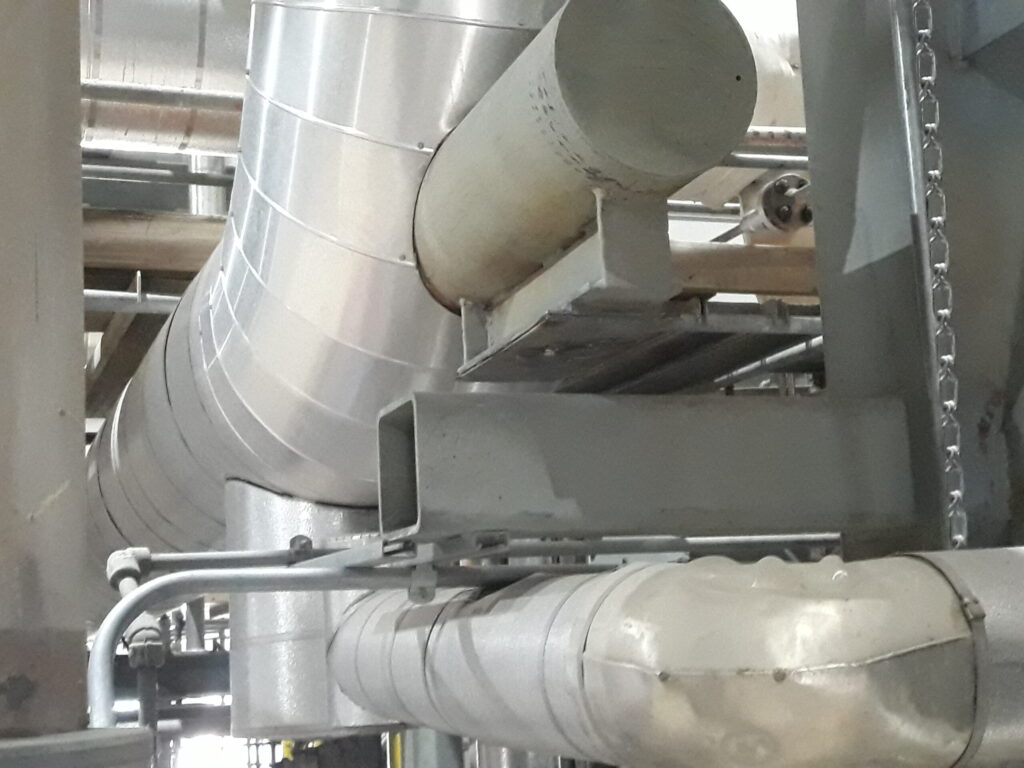
During my time at the power plant, it was noticed that I was quite good at catching issues that others missed before they turned into bigger problems. Because of this, they decided to have me do a plant-wide piping and piping support inspection. This inspection took about 2 weeks to complete, but I was able to find many things that needed some attention. During this inspection I was able to locate and make recommendations on a number potential problems I found, including one that was determined to be serious enough that scaffolding was special ordered and rushed to the site within an hour to prevent a major steam pipe from potentially failing on the primary base load 2×1 block. Less serious things were simply added to my report for review.
Unit 4/5 Unplanned Outage
Because I was taking summer classes while I worked at the plant, my hours were a bit different than the other engineers. One day I ended up being the only one on site when the technicians needed an urgent CAD drawing to send to a gasket manufacturer after a gas turbine had to be taken offline for a failed gasket.

I had not been at the plant very long at the time and had only just started to learn how to use AutoCAD (previously I only had experience with SOLIDWORKS). After a technician brought me a drawing with rough dimensions on a piece of cardboard, I was able quickly learn the program and to transfer those dimensions as well as dimensions I went and measured on the unit to the CAD model to send off that evening for manufacture. This ultimately resulted in the unit’s downtime being significantly reduced.